
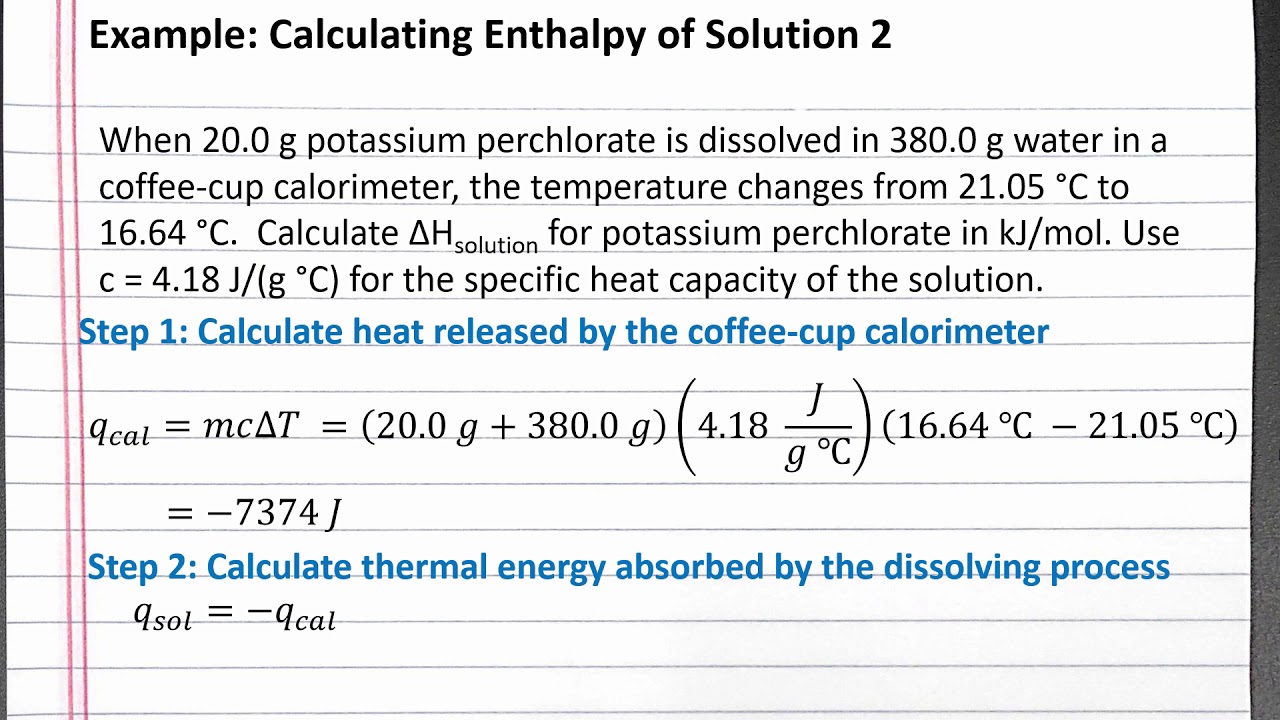
Joules and calories and kilocalories: A calorie is defined as theĪmount of energy required to raise the temperature of 1 g of water fromĤ.184 J = 1 cal all food 'calories' are really kcal. Kilo and kelvin: write k for 1000's and K for kelvin. This definition means that theįreezing temperature of water is 273.15 K. Temperature at zero pressure where the volumes of all gases is
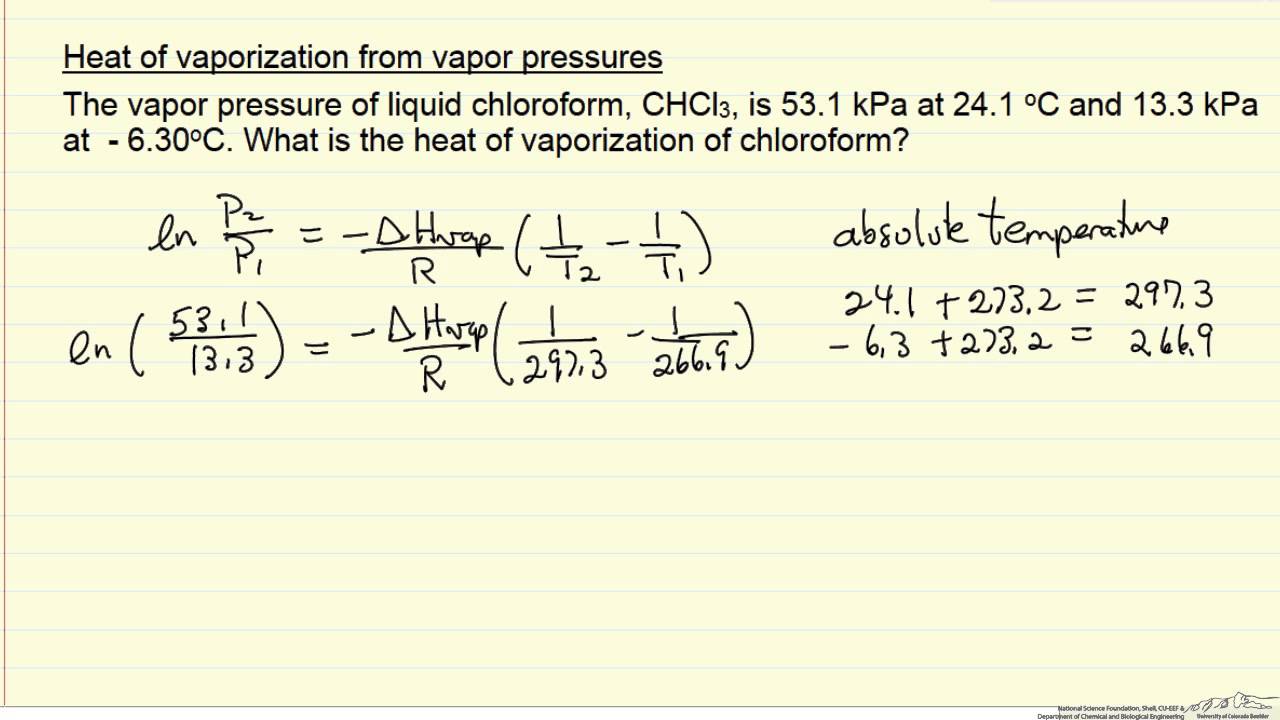
The Kelvin scale is based on defining 0 K, "absolute zero," as the The Celsius scale is based on defining 0 ☌ as the freezing point of water and 100☌ as the boiling point. Units of Temperature: Degrees Celsius and Kelvin
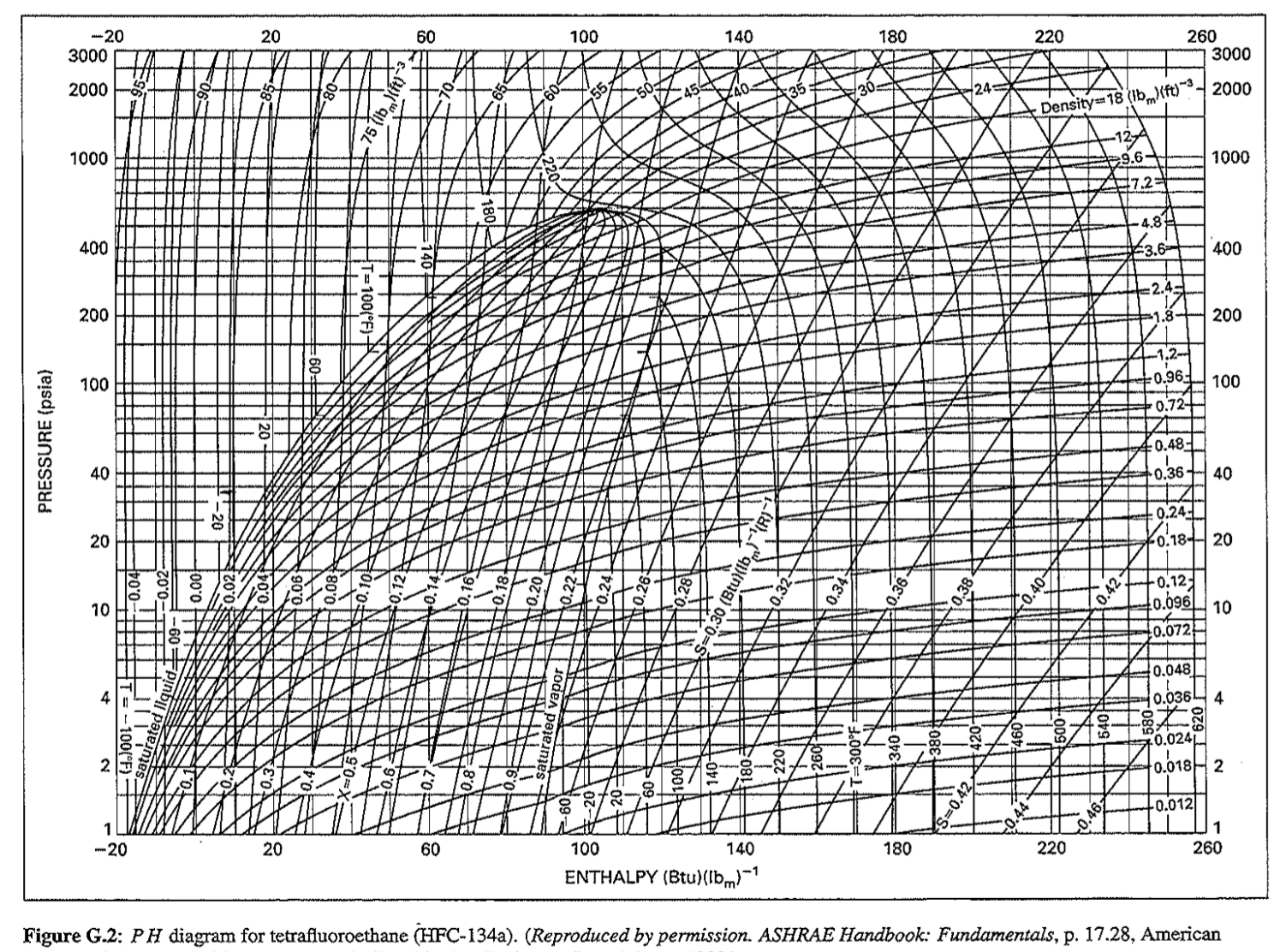
(90%) and a small number of indirect consumers (c = 10%) so that hardly any oxygenic condensate returns. Steam system consisting mainly of direct consumers The make-up water is replenished from an osmosis water treatment unit and the boiler has a low salt mode of operation. (c = 90%) and a small number of direct consumers (10%).

Steam system consisting mainly of indirect consumers If the heat loss in the pipework is precisely calculated, the steam demand for these losses must be determined in the same manner as the heat demand for an indirect consumer. The insulation of pipework (both in the steam and also the condensate system) represents one of the most economical cost-saving measures in existing systems. This is mainly the case because during the service life of the system, the insulation is removed for inspection or maintenance and not reinstalled afterwards. Unfortunately the heat loss via poorly or only partially insulated pipework, containers and valves is still underestimated. Corresponding guide values can be found in the chapter Efficiency. The heat losses at valves, flange connections and containers must also be taken into account accordingly. To calculate heat losses more accurately, a separate calculation must be carried out for every pipe run based on the nominal diameter, length of the pipe and insulation thickness. If the pipework is well insulated, a heat energy demand of roughly 10kg steam per hour and in each pipe (10kg S / (h The heat loss in the pipework must also be taken into account in the steam output design.
